100% polyester chemical fiber imitation batik fabric clothing fabric super wax african style microfiber
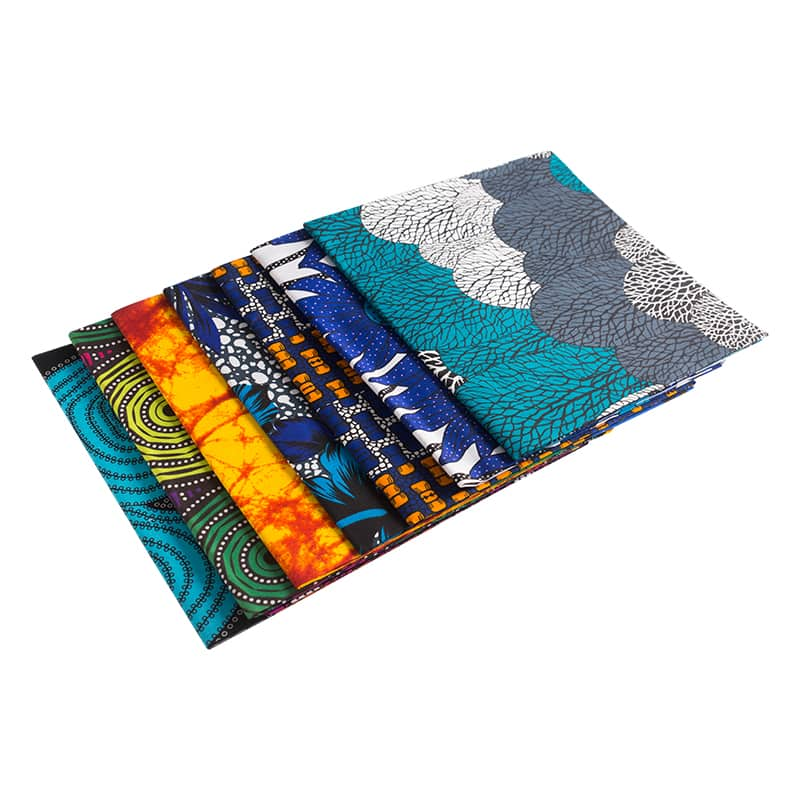
Most of our polyester fabrics are used in the production of home textile products, which are the raw materials of home textile products. There are thousands of design drawings for customers to choose from. They have a soft feel and strong quality, and can provide products of different specifications according to customer needs.
These substances are mixed with the fabric and then heated in a bath containing 1.2% dye.The resulting fabric exhibits an improved color and dimensional properties. It also shows a slight decrease in tensile strength.The dye concentration in the dyebath increases the permeation of the dye to the fiber. In addition, higher exhaustion increases the amount of dye present in the fiber.During the dyeing process, hydrophobicity of polyester fiber restricts the diffusion of dye molecules into the fiber interior. However, this limitation is overcome when the fiber is dyed at a high temperature. This results in a greater absorption of dye by the fiber, which increases the depth of shade of the fabric.The crystalline nature of polyester fiber also restricts the uptake of water molecules. This can be remedied by various methods. A protease enzyme can break down the epicuticle, which provides a hydrophobic barrier at the surface of the fiber.A scanning electron microscope can show whether or not the fiber has changed during the dyeing process. The resulting images can be compared with the undyed fiber.
The dyed samples showed staining onto the multifiber fabric, but not on the other polyester fabric.Using a formaldehyde free discharge agent on polyester dyed fabric will permanently destroy the chromogenic system of the fibre. This will result in an unsightly discolouration.During discharge printing, a fabric is first dyed with a solid colour, then printed with a colouring material containing a discharging agent. This is done in a bath of steam at 102 deg-104 deg C for several minutes. The colour is then removed by washing off the stage.Discharging agents are chemicals that are used to break up or remove colouring materials such as pigments, dyestuffs and whites. They are usually acid or alkalis. They can also be used to strip dyes from a fabric. They should be used with appropriate safety precautions.Most discharging agents are oxidising or reducing agents. Sodium formaldehyde sulphoxylate is the most widely used. It is available as Rongalite C (BASF) or Formosul. Zinc formaldehyde sulphoxylate (Decrolin) is another reducing agent.Using the dye extracted from henna leaves is an eco-friendly method to color polyester fibers without the use of metallic mordants. This approach is a promising one because it enables an efficient, environmentally friendly dyeing process.The results indicate that dyeing polyester fiber with henna dye at high temperature is not harmful to the physical properties of the fiber.
The dye particles penetrate deep into the fiber's interior and provide strong coloration. Moreover, the fiber's surface structure remains unchanged after processing at an elevated temperature.The fastness properties of the henna dye were satisfactory. The fabric dyed with henna at 130 degC shows a longer bar compared to that of fabric dyed at 120 degC. In addition, the dyed fabric samples showed good colorfastness to washing and rubbing.Using a plastisol based composition can help to prevent dye migration from your polyester dyed fabric into your print. This is particularly useful on dark fabrics. Its hydrophobic nature makes it less likely for the dye to migrate into the plastisol based composition.It can also be used on a 50/50 blend of cotton and polyester. It can be a great way to print on a fabric that was not originally designed for printing.It can be cured at a low temperature, 280 degrees Fahrenheit. This helps save energy and protects the environment. Typically, a low-cure plastisol ink is more expensive than a regular plastisol ink, but it is a great choice for the environment.A low-cure plastisol ink can be made by adding a low-cure additive to any plastisol ink. These additives can lower the cure temperature to 280 degrees. This will make the colors look brighter. Using a low-cure ink also helps to prevent gas migration.